✕
During the pandemic, training couldn’t stop. HVAC contractors had to figure out a way to keep their employees safe while also keeping their skills sharp. To do this, they introduced hybrid and remote learning, and many people wondered if this type of learning was the new “norm.”
Fast-forward a couple of years and it’s largely back in-person, although many HVAC educators today still pair the two.
At Bradford White’s For The Pro Training Academy in Middleville, Michigan, the focus is hands-on training, supplemented by virtual live presentations, on-demand video content, and self-guided learning.
“We have a 5 million BTU live fire lab here in the facility, where they teach products overviews, and a sequence of operation, where we break and fix those good things,” said Spencer Pope, supervisor of technical training and tech support at Bradford White.
With the modern hydronics training done by Bradford White’s subsidiary, Laars Heating Systems, it’s a similar approach. Steven Moruzzi, national training manager for Laars Heating Systems, conducts boiler trainings at iTEC, Bradford White’s international technical center in Middleville, Michigan, as well as trainings at Laars and rep locations as requested.
Here is how two hydronics manufacturers are handling training their techs.
Hybrid Strategies
Today’s HVAC training centers cover an array of topics, using a variety of different methods, and knowing which type of training to pick can be a little overwhelming for those coming up in the industry.
“I think that a big portion of training is audience definition, and that’s something that our team here at Bradford White works really hard on — is asking questions like what’s their motivation to pursue the training, what are their interests and goals, what challenges are bringing them to us? And then, what’s their profession?” Pope said. “Are they looking for technical content because they are a contractor? Are they in the sales or support side of the industry?”
Whatever the answer, Bradford White will tailor its content accordingly. They’ll also ask questions about the trainee’s knowledge and skill level.
“If we do have new technicians that are in the trades, what we tend to find is that they come in fairly green,” Pope said. “We don’t maybe have as much infrastructure that supports newer technicians and feeds them into the trades, and so we find with our program that we want to start with some of those core fundamentals, or those foundational concepts, just to make sure we are covering everything that we need to cover to make the best technicians.”
Part of ensuring technicians learn everything necessary to succeed in their careers is staying on top of industry advancements by adapting new training strategies — and, when needed, dropping dated ones.
Bradford White takes a hybrid approach here.
“Part of that conversation leads into ROI, not only for a business owner who is choosing to either send their technicians to our facility, or even taking the time out just to have the technicians take an hour-long virtual presentation at their own shop, but it’s also about reaching students where they are and using technologies they are comfortable with,” Pope said.
Likely the best way students will retain information is through hands-on training.
“But when we’re looking at reaching students with a hybrid approach, we’re doing something like a live virtual presentation, where maybe our rep agency goes and they get parts in the hands of the technicians at their shop,” he explained. “Then we, as technicians and trainers, get on camera and call on students, have them put their hands on parts and use their own tools and do some hands-on troubleshooting, but in a virtual classroom.”
At Laars, product training has been a core belief since it was founded in 1948, and it’s taken on many different forms over the years.
“Our modern curriculum took shape starting in 2011 when we built the Laars Customer Center dedicated to live fire product trainings,” Moruzzi said. “Training has expanded to include an online series via the Laars Academy, where technicians can expand their knowledge through various hydronics and product tutorials.”
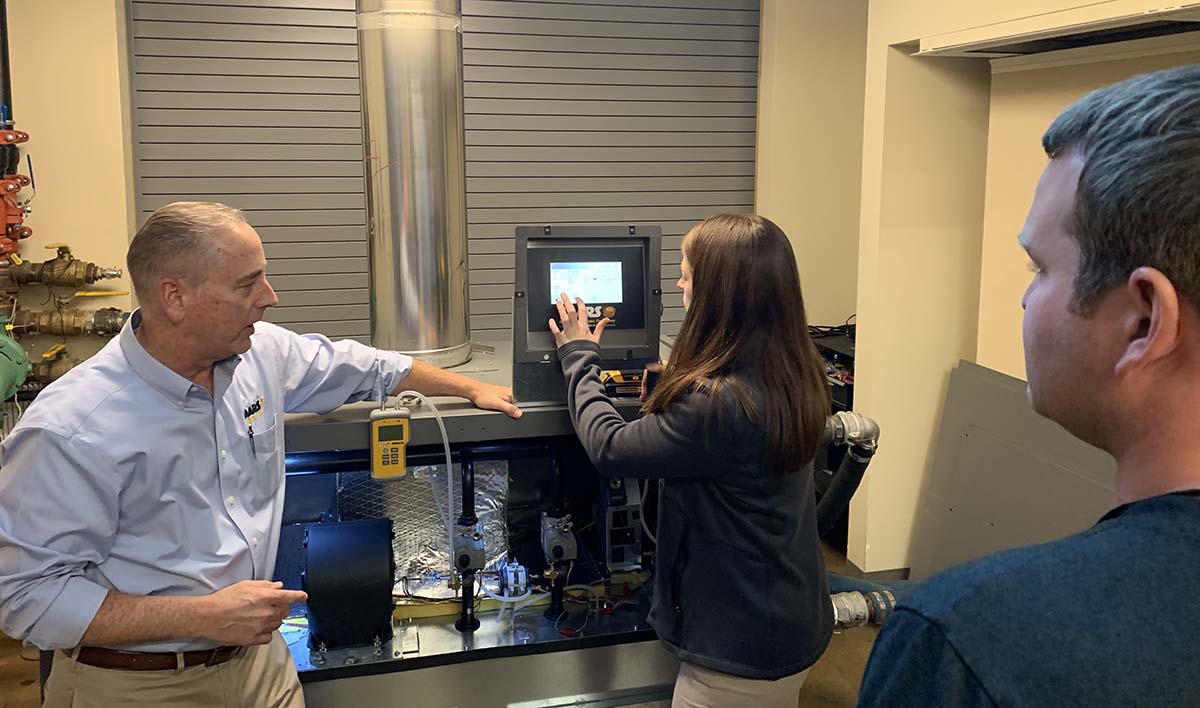
INTERACTION: The Laars Customer Center offers interactive training that covers things like hydronic system piping, proper installation and venting techniques, hands-on programming, live fire troubleshooting, and more. (Courtesy of Bradford White)
Training Challenges
Pope said the biggest challenge trainers face is getting the industry to see the value in consistent training. He said it goes back to establishing the ROI side of it for both the business owner and their technicians.
“The best way I could help establish an ROI is talking about one of the approaches we have at Bradford White — a ‘rising tide raises all ships’ kind of concept,” Pope said. “If we teach universal troubleshooting concepts — if we teach technicians the fundamentals of venting or sequence of operation that would technically apply across the spectrum of gas or electric products — they come away from our trainings with a marketable skill set for themselves as individuals … and they come away more confident so that they could apply these skills to not only a water heater, but potentially to a boiler or to other pieces of equipment.”
Meanwhile, what a business owner gains from their technicians undergoing the right type of training is more confident technicians and increased efficiency on each job — which translates to more customers.
When Bradford White takes students into their classes, they teach them a sequence of operation on live fire equipment. They break the students into very small groups so that everybody gets their hands on the equipment. Then, they have the students diagnose, troubleshoot, and repair the water heaters based on all different scenarios.
“And what we’ll do is measure how long it took each to diagnose, troubleshoot, and repair a problem when they first started and didn’t quite know what they were doing … and then at the end of our session together, we do one last round where they go back to the same station they worked on before, and what we have found so far this year is an average of over 550% decrease in that diagnosis, troubleshoot, and repair time,” Pope said.
Having that kind of data point provides a tangible example to both technicians and contractors of the value of that training.
“Even a virtual class that’s just one hour long — it’s important for us to help provide those metrics to show there are skills gained, and there’s definitely an ROI on the stuff,” Pope said.
Moruzzi said technology is constantly changing, and one of the challenges facing hydronics training is how difficult it can be for everyone involved to keep up with the latest training techniques and methods.
“There is a learning curve for technicians just starting out and plenty of continual learning, even for us industry veterans,” said Moruzzi.
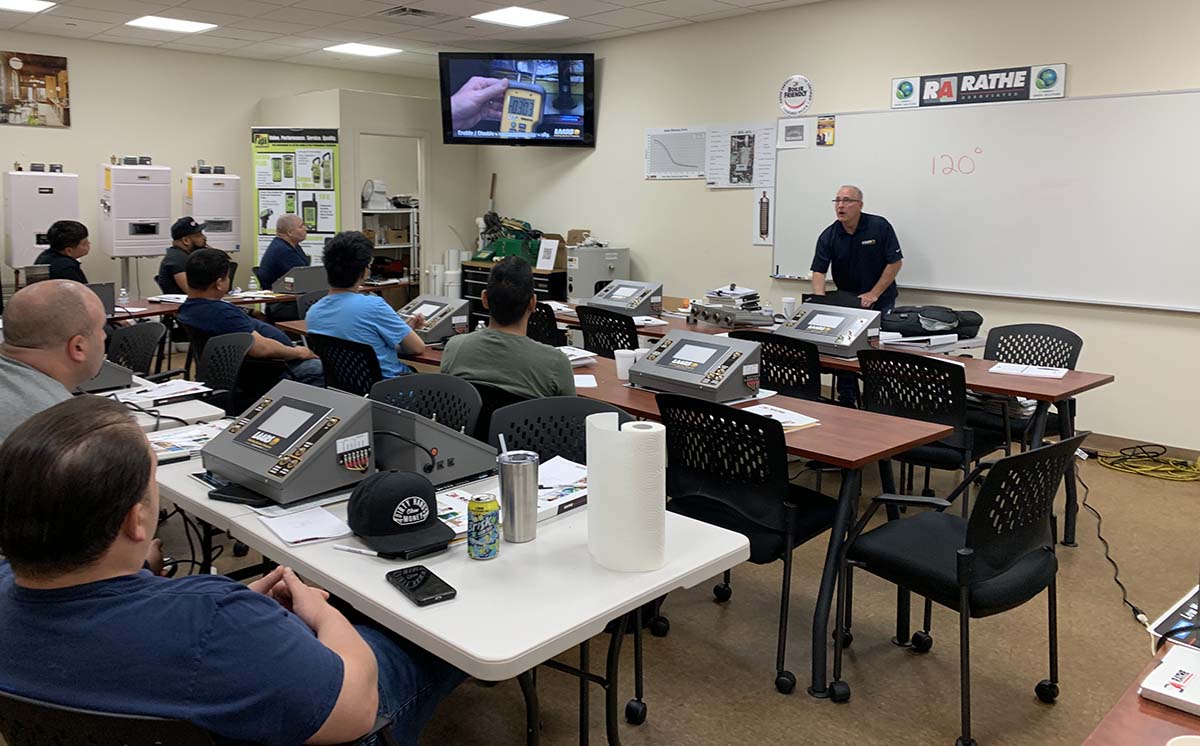
CONTINUAL LEARNING: There is plenty of continual learning required from trainers to keep training methods current. (Courtesy of Bradford White)
Hydronics Training
Technicians who choose Laars for their hydronics training will have the opportunity to learn about things like hydronic piping concepts, proper sequence of operations for Laars boilers and water heaters, combustion setup, control programming, safety and lockout conditions, and troubleshooting.
“In the Laars Customer Center, we offer interactive training that covers hydronic system piping, proper installation and venting techniques, hands-on programming, live fire troubleshooting, service, and combustion analysis,” said Moruzzi said. “It is critical that installers understand how each type of heating appliance operates and proper installation practices. This ensures that the heating system is installed safely and properly, allowing for long, efficient operation.”
Whether you require installation, repair, or maintenance, our technicians will assist you with top-quality service at any time of the day or night. Take comfort in knowing your indoor air quality is the best it can be with MOE heating & cooling services Ontario's solution for heating, air conditioning, and ventilation that’s cooler than the rest.
Contact us to schedule a visit. Our qualified team of technicians, are always ready to help you and guide you for heating and cooling issues. Weather you want to replace an old furnace or install a brand new air conditioner, we are here to help you. Our main office is at Kitchener but we can service most of Ontario's cities
Source link