This story is about good intentions gone bad during a VRF installation for a new 73,890 square for LEED Platinum middle school that opened in the fall of 2017. The construction cost was $30 million, the school was awarded recognition as the first Net Zero school in Illinois as well as numerous additional accolades.
The district was told a VRF system would be very efficient and provide years of reliable service with little maintenance. Unfortunately, the story goes south quickly, and the honeymoon period ended badly. So, what went wrong?
The initial design was a different manufacturer, but the product exceeded the budget and wouldn’t accommodate the schedule, so an alternate was selected. Unfortunately, the drawings were never updated, and the as-built submitted drawings were the schematic design drawings for the original manufacturer. There was commissioning and a design engineer for the project, but this wasn’t caught.
During the installation, the manufacturer representative wasn’t monitoring the installation nor the startup because they were unavailable. With no as-built drawings, it was impossible to properly determine the correct refrigerant charge because every manufacturer has a program that the piping is entered into and the proper charge is determined. During the equipment startup, the refrigerant charge for a system was lost because during the brazing process shraeder o-rings were melted and the refrigerant charge leaked out.
The spring of 2018, compressors started failing, but none were ever tested to determine the reason. It is assumed the reason was poor brazing techniques with out nitrogen, which creates Cubric Oxide, which leads to clogs and premature system failure. None of the 28 replaced compressors was ever diagnosed to determine the failure, which is poor workmanship. There was no troubleshooting to determine the failure, only equipment replacement to continue charging the client for labor and material.
The manufacturer was contacted numerous times, requests for them to visit the site were refused and the Owner left frustrated. The manufacturer representative failed to have the equipment checklists completed, thus the manufacturer had no record the equipment was even installed. Still, the manufacturer should have questioned why material shipped before and after was registered and this batch of equipment not. The manufacturer representative continued supplying replacement compressors but stopped in the spring of 2024.
Improper installation of the condensing units from too little clearance, installing near adjacent walls that exceed the height of the condensing unit, not considering the snowfall clearance, or future maintenance were all overlooked with this project. Add in piping the condensing unit from the front (allowed per manufacturers but it is the least preferred), insufficient piping supports caused dips and traps which prevent the proper migration of oil back to the compressor.
The manufacturers training manual states “it is best to keep piping clear of service access panels, or it is sure to get stepped on and damaged”. The manufacturer is limited to the end user training provided by the manufacturer representative, and additional oversight needs to be exercised here. See figure 1.
The installing contractor needs to complete training by the manufacturer to become certified to install the equipment. The industry needs to start certifying electrical contractors to follow the manufacturer’s guidelines as well. The installation manual manufacturers develop is only as good as the training provided to the installing contractors, and this phase needs to be improved upon. Of our eight condensing units, only two had dedicated fused disconnect or breaker each, while the remaining six condensing units in a paired configuration of three condensing units only had two breakers. Figure 2 shows the supply electrical and communication conduit entering. There are 4 conduit openings, and the manufacturer requires the openings be used opposite each other, so upper left lower right, etc., not side by side. (Figure 2)
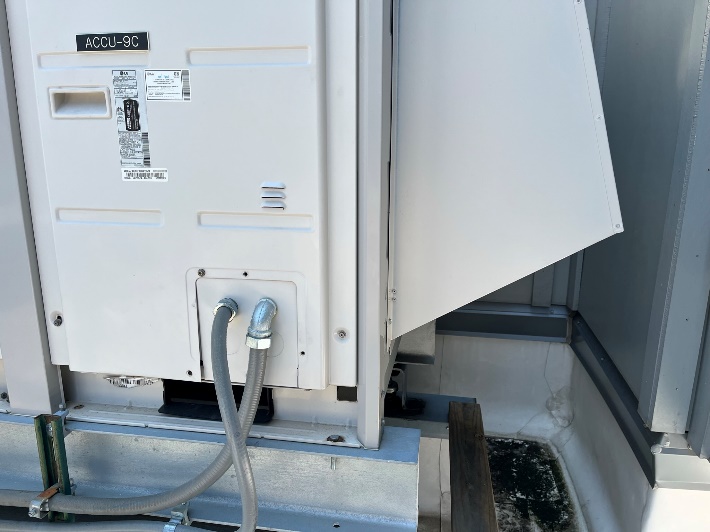
This ensures the power wiring is a minimum of two (2) inches away from the communication cabling to avoid operation problems caused by electrical interference. (Figure 3). Unfortunately, the following sentence in the installation manual says if it is necessary to run the power wiring and communication cable alongside each other and cannot be avoided there is a table provided of separation minimum allowable distances with the minimum distance 11 13/16” up to 59 1/16”.
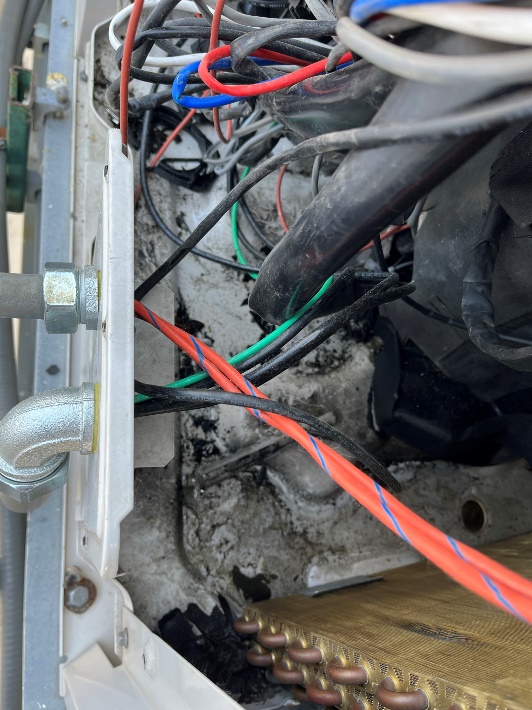
The installation manual further states “When connecting the power wiring and communication cables, avoid placing these near the oil level sensor. If placed near the sensor, electromagnetic energy may cause the sensor to malfunction. The condensing unit that experienced the most compressor failures upon inspection we found the oil level sensor wiring was intertwined with the power and communication cabling.
There are a few key points I would like you to take away for your next project:
Piping to the HR box from the Condensing Unit
This piping is the most important for proper operation. The piping needs to be hard ACR Tubing, properly supported every 10 feet horizontally and vertically, installed sloped away from the condensing unit down towards the heat recovery box. The piping needs to installed level with no dips or traps and ensure the pipe at the condensing unit has sufficient supports, which our example didn’t. Dips and traps collect oil and prevent the proper migration back to the compressor, thus causing a compressor failure.
Clearance
Whether it is a heat recovery box in the ceiling or the condensing unit, all manufacturers have guidelines to follow. It is best to differ to the maximum distance suggested, for side and rear clearance and clearance between adjacent condensing units. One manufacturer recommends “Generally 3 foot clearance all around units is ideal.” I second that recommendation for proper airflow, system capacity and maintenance access.
Ensure every instillation individual for the mechanical contractor is trained and certified in the manufacture installation procedure.
As the Owners Advocate, you need to champion on their behalf that every individual installing the VRF system has participated in the manufacturers training program, is certified and understands the importance of following the manufactures installation procedure fully. Ensure the general contractor understands the importance and request their assistance in verifying every employee of the mechanical contractor is certified by the manufacturer for a proper installation.
Document, document, document. Be detailed, ask questions, don’t accept the status quo.
This topic was delivered as part of the ACG Essential Cx Webinar Series. Save the Date for ACG’s CxEnergy 2025 Conference & Expo, the premier event in commissioning, building technology, and energy management (April 28-May 1, Charlotte, NC).
Whether you require installation, repair, or maintenance, our technicians will assist you with top-quality service at any time of the day or night. Take comfort in knowing your indoor air quality is the best it can be with MOE heating & cooling services Ontario's solution for heating, air conditioning, and ventilation that’s cooler than the rest.
Contact us to schedule a visit. Our qualified team of technicians, are always ready to help you and guide you for heating and cooling issues. Weather you want to replace an old furnace or install a brand new air conditioner, we are here to help you. Our main office is at Kitchener but we can service most of Ontario's cities
Source link