✕
The CO2 refrigeration era is upon us.
The CO2 refrigeration market, which was valued at $3.2 billion in 2022, is expected to reach $7.5 billion by 2030. The installation of transcritical CO2 systems is expected to increase by 176% by 2028. This immense growth is on display in numerous supermarket chains, which have either pledged their intentions to rely heavily on CO2 going forward.
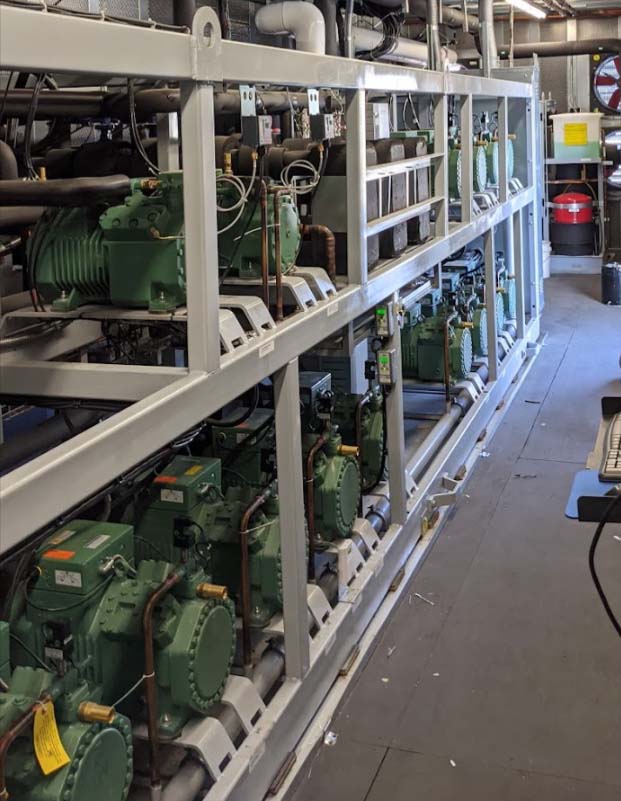
COMFORT CENTER: A CO2 refrigeration rack providing refrigeration, air conditioning, and heating for a facility in Sunnyvale, California. (Image courtesy of Effecterra)
CO2 is a popular choice because of its efficiency, offering an average of 10% more energy savings compared to traditional HFC parallel-rack systems. In some cases, energy consumption can be reduced by as much as 58%, as demonstrated by a Norwegian SPAR supermarket case study.
Alongside these energy savings, the use of CO2 refrigerants offers significant financial advantages. With traditional refrigerant prices having more than tripled in recent years, supermarkets can save up to 80% on refrigerant costs. Additionally, CO2 systems require less maintenance and have a lower total cost of ownership (TCO), making them a compelling choice for the future of refrigeration.
All of this data paints a promising future; however, the question remains: who’s going to install and maintain all of these R-744 systems?
The Rising Demand for CO2 Refrigeration
Environmental regulations and consumer demand have pushed CO2 refrigeration (R-744) – and its extremely low global warming potential (GWP) of 1 — into the limelight, making it a frontrunner in the refrigeration space. However, like any significant shift in technology, the transition requires education, adaptation, and careful consideration of its complexities.
Peter Savage, project manager, controls division, AAA Refrigeration Service Inc., in Bronx, New York, said his company jumped on the bandwagon nearly a decade ago.
“When we first took on CO2 in 2015, the biggest concern was the high pressures compared to what we were used to,” he said. “But we took all the necessary precautions — trained our technicians, worked with Hill Phoenix, and kept up with ongoing training. You can’t go in blind, especially with something so new.”
For technicians accustomed to working with traditional refrigeration systems, these high pressures can be intimidating. But, as Peter Savage explains, with proper training, technicians can adapt.
“We made sure that our techs were exposed to the system early on and followed all the piping best practices,” he said. “The mistake we made was creating dry ice in the system because our technicians weren’t fully aware of CO2’s unique characteristics. It was a learning moment, and they adapted quickly once they understood the importance of pressurizing with vapor first.”
Savage admits that his team had to encounter CO2’s hurdles in person to truly conquer them.
“High-pressure refrigerants, such as CO2, require technicians to think differently,” he said. “With such complex control systems, one wrong adjustment, like changing a setpoint, can lead to system malfunctions. It’s hard to comprehend each step from a book – you have to go out and actually get your hands on the system to truly learn how it works.”
Brett Wetzel, director of strategic technical services and solutions, Future Green Now, and host of the Advanced Refrigeration Podcast, said classroom work is important but nothing trumps putting that knowledge to the test on-site.
“Issues like the creation of dry ice within the system can severely damage components,” he said. “When techs learn the triple point and how and when CO2 changes states, the systems become much easier to maintain.”
Always Evolve Your Curriculum
Mark Doninelli, vice president, Estes Refrigeration, said his team is constantly altering its training, ensuring techs are ready and willing to tackle all CO2-based challenges.
“We strive to equip techs with the right tools and knowledge to handle these systems,” he said. “Every year, we update our curriculum to keep pace with new technology and feedback from our team. But it’s also about getting hands-on experience. It’s one thing to learn in the classroom, but the real value comes when technicians can apply that knowledge in the field.”
This philosophy of continuous improvement is not just about teaching the basics — it’s about fostering an environment where technicians are comfortable troubleshooting and learning from their experiences.
“Working with CO2 requires a different kind of mindset,” said Savage. “Mastering the controls is a challenge that becomes easier with experience. But, the controls technology is always changing, so we must make sure our training evolves as well.”
Wetzel encouraged techs to simply give it a shot and to learn from their failures.
“CO2 systems can look intimidating, but once technicians understand how to work with them, it’s much more straightforward,” he said. “As a trainer, I’ve learned that giving techs real-world problems to solve in a safe training environment makes all the difference. If they can get their hands on a system and try it out, that’s when the real magic happens.”
Understanding the Unique Components of CO2 Systems
CO2 systems come with a host of new components and design considerations. Understanding how CO2 systems behave; their unique components, like flash bypass valves and high-pressure valves; and then comprehending what each component does and how they all interact with one another can make CO2 much less intimidating.
“The challenges within CO2 systems are similar to most other refrigeration systems in terms of troubleshooting,” said Adam Dykstra, refrigeration operations manager, DeTroye Electric Service, Oostburg, Wisconsin. “It’s still a refrigeration system at its core.”
Don’t let the flashing of CO2 as it transitions from liquid to gas intimidate you, said Wetzel. “Ensuring that everything is properly sized and that those transitions are occurring as they’re supposed to will effectively help you prevent failures.”
The Future of CO2 Refrigeration
CO2 refrigeration is no longer a vision of the future — the gas has arrived and is here to stay.
“CO2 has the lowest GWP available, which is critically important,” said Savage. “Yes, ammonia is another low-GWP option, but it requires more stringent safety measures, and then there’s the flammability risk with things like propane. CO2 is the safer, more versatile choice.”
Doninelli echoed this sentiment, stating CO2 refrigeration is on the cusp of widespread adoption in the U.S.
“The more we work with CO2, the more we see its advantages, especially in urban settings,” he said. “It’s compact, highly efficient, and safer compared to some of the other low-GWP options.”
Wetzel agreed, noting the refrigerant’s efficiency as a hallmark attribute.
“The increasing usage of CO2 refrigeration isn’t just about environmental benefits — it’s about efficiency and system longevity,” he said. “Once the training is in place and the kinks are worked out, CO2 systems are often a more reliable and cost-effective solution than traditional systems.”
Moving Forward with CO2 Systems
The path to CO2 refrigeration system mastery is lined with obstacles, but with the right training, resources, and mindset, HVAC technicians can succeed.
“It’s all about the right approach — train your team, get hands-on experience, and understand the system’s nuances,” said Dykstra. “Once you have that foundation, troubleshooting becomes easier.”
A company’s success hinges on a technician’s ability to understand both the theoretical and practical aspects of the technology, said Wetzel.
“Training alone isn’t enough,” he said. “You need to make sure technicians can work with these systems in real-world scenarios. That’s the only way to really prepare them.”
The future of commercial refrigeration runs on R-744 and, for HVAC contractors, that future has arrived. By embracing new technology and committing to continuous learning, technicians can navigate the complexities of CO2 systems and ensure that they remain at the forefront of an industry that’s increasingly focused on sustainability and efficiency.
Whether you require installation, repair, or maintenance, our technicians will assist you with top-quality service at any time of the day or night. Take comfort in knowing your indoor air quality is the best it can be with MOE heating & cooling services Ontario's solution for heating, air conditioning, and ventilation that’s cooler than the rest.
Contact us to schedule a visit. Our qualified team of technicians, are always ready to help you and guide you for heating and cooling issues. Weather you want to replace an old furnace or install a brand new air conditioner, we are here to help you. Our main office is at Kitchener but we can service most of Ontario's cities
Source link